Are you struggling to keep track of your inventory? Does your current system leave you with inaccurate data and wasted time? If so, you’re not alone. Many businesses face these challenges, but the good news is that ERP software can provide a solution. This article will explore the benefits of ERP software for inventory management, showing how it can streamline your processes, improve accuracy, and ultimately boost your bottom line. We’ll discuss how ERP can help you manage inventory levels, track stock movements, and optimize your supply chain. If you’re looking to take control of your inventory, read on to discover how ERP software can empower your business.
The Challenges of Traditional Inventory Management
In the ever-evolving landscape of business, maintaining an efficient and effective inventory management system is paramount. Traditional methods, however, often face significant challenges that can impact profitability and customer satisfaction.
1. Inaccurate Inventory Data
One of the most prevalent challenges is inaccurate inventory data. Manual data entry, human error, and outdated systems can lead to discrepancies between physical inventory and records. This can result in stockouts, overstocking, and lost sales.
2. High Storage Costs
Traditional inventory management often involves large warehouses and significant storage costs. Maintaining a substantial inventory can be expensive, especially for perishable goods or items with high obsolescence rates.
3. Slow Order Fulfillment
Manual processes and limited visibility into inventory levels can lead to slow order fulfillment times. This can frustrate customers and erode brand loyalty.
4. Difficulty in Forecasting Demand
Predicting future demand accurately is crucial for effective inventory management. Traditional methods often rely on historical data and subjective estimates, which may not account for market fluctuations, seasonality, or emerging trends.
5. Lack of Real-Time Visibility
Traditional inventory management systems often lack real-time visibility into inventory levels and movements. This makes it difficult to track stock in transit, manage stock allocation, and respond quickly to changes in demand.
To overcome these challenges, businesses are increasingly turning to modern inventory management solutions that leverage technology such as cloud computing, data analytics, and artificial intelligence. These solutions offer enhanced accuracy, visibility, and efficiency, enabling businesses to optimize their inventory processes, reduce costs, and improve customer satisfaction.
How ERP Software Revolutionizes Inventory Control
In today’s fast-paced business environment, efficient inventory management is paramount to success. Traditional methods often struggle to keep up with the complexities of modern supply chains, leading to stockouts, overstocking, and ultimately, lost revenue. This is where Enterprise Resource Planning (ERP) software comes into play, offering a comprehensive solution to optimize inventory control and streamline operations.
Real-Time Visibility and Data Accuracy
One of the key advantages of ERP software is its ability to provide real-time visibility into inventory levels. Unlike manual systems, which often rely on outdated data, ERP systems constantly update inventory information as transactions occur. This ensures that businesses have access to accurate data at all times, enabling better decision-making and preventing stockouts or overstocking.
Automated Inventory Tracking and Management
ERP software automates many inventory management processes, significantly reducing the workload of staff. From receiving and storing goods to picking and packing orders, ERP systems streamline these tasks, minimizing errors and increasing efficiency. This automation also frees up valuable time for employees to focus on strategic activities.
Improved Demand Forecasting and Planning
ERP software leverages historical data and advanced algorithms to provide accurate demand forecasting. By analyzing past sales patterns, seasonal trends, and other relevant factors, ERP systems generate reliable projections, enabling businesses to plan production and procurement more effectively. This reduces the risk of stockouts and ensures that businesses have the right inventory on hand to meet customer demand.
Enhanced Order Fulfillment and Delivery
With a centralized database and automated processes, ERP software enhances order fulfillment and delivery. Businesses can track orders in real-time, monitor shipment progress, and ensure timely delivery. This improved efficiency enhances customer satisfaction and strengthens brand reputation.
Cost Savings and Increased Profitability
By optimizing inventory control, ERP software contributes to significant cost savings. Businesses can minimize storage costs, reduce waste due to expired products, and lower transportation expenses. These cost reductions translate into increased profitability and a stronger financial position.
Conclusion
ERP software is a powerful tool that can revolutionize inventory control, enabling businesses to achieve greater efficiency, accuracy, and profitability. By providing real-time visibility, automating processes, and improving demand forecasting, ERP systems empower organizations to make informed decisions and optimize their supply chains for success.
Real-Time Inventory Tracking and Visibility
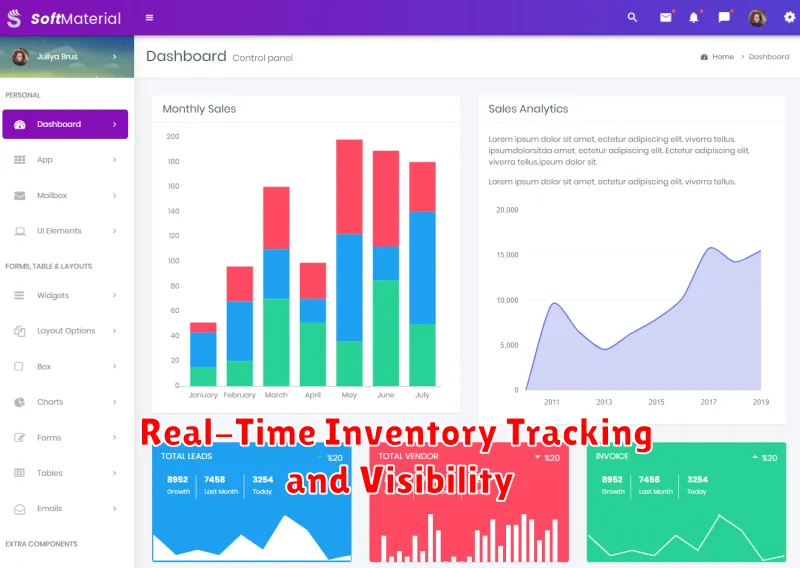
Real-time inventory tracking and visibility is a critical component of modern supply chain management. It provides businesses with up-to-the-minute insights into the location and status of their inventory, allowing them to make better decisions about production, distribution, and fulfillment.
With real-time inventory tracking, businesses can:
- Reduce stockouts and overstocking by ensuring that they always have the right amount of inventory on hand.
- Improve order fulfillment times by knowing exactly where inventory is located and when it will be available.
- Optimize inventory management by identifying slow-moving and obsolete inventory.
- Gain a competitive advantage by providing customers with accurate and timely information about product availability.
How Real-Time Inventory Tracking Works
Real-time inventory tracking typically relies on a combination of technologies, including:
- Radio Frequency Identification (RFID) tags: These tags are attached to inventory items and emit radio waves that can be detected by readers. This data is then transmitted to a central database.
- Barcode scanners: Barcode scanners are used to scan barcodes on inventory items, which allows for quick and easy tracking of inventory movement.
- Global Positioning System (GPS) tracking: GPS tracking devices can be used to track the location of inventory items in transit.
- Internet of Things (IoT) sensors: IoT sensors can be used to monitor environmental conditions, such as temperature and humidity, which can affect inventory quality.
- Cloud-based software: Cloud-based software solutions are used to collect, store, and analyze data from these technologies, providing businesses with real-time insights into their inventory.
Benefits of Real-Time Inventory Tracking
The benefits of real-time inventory tracking are numerous, including:
- Increased efficiency: By knowing where inventory is located and when it will be available, businesses can optimize their supply chain processes.
- Reduced costs: Real-time inventory tracking can help businesses reduce stockouts and overstocking, which can significantly reduce inventory-related costs.
- Improved customer satisfaction: By providing customers with accurate and timely information about product availability, businesses can improve customer satisfaction and loyalty.
- Better decision-making: Real-time inventory tracking provides businesses with the data they need to make informed decisions about production, distribution, and fulfillment.
Conclusion
Real-time inventory tracking is essential for businesses that want to optimize their supply chains, improve customer satisfaction, and gain a competitive advantage. By embracing these technologies, businesses can gain valuable insights into their inventory and make better decisions about their operations.
Automated Inventory Replenishment and Order Management
In today’s fast-paced business environment, efficiency and accuracy are paramount. Automated inventory replenishment and order management systems are essential for businesses of all sizes, allowing them to streamline operations and optimize inventory levels. These systems utilize advanced technology to automate key processes, freeing up valuable time and resources for other crucial tasks.
Benefits of Automated Inventory Replenishment and Order Management
Implementing an automated system brings numerous benefits, including:
- Reduced inventory costs: By optimizing stock levels, businesses can minimize holding costs, reduce waste due to expired products, and prevent overstocking.
- Improved order fulfillment accuracy: Automated systems minimize human error, ensuring that orders are processed correctly and delivered on time. This leads to greater customer satisfaction and loyalty.
- Enhanced visibility and control: Businesses gain real-time insights into inventory levels, stock movement, and order status, allowing them to make informed decisions.
- Increased efficiency: By automating repetitive tasks, businesses free up employees to focus on higher-value activities such as strategic planning and customer service.
- Improved responsiveness to market fluctuations: Automated systems can quickly adapt to changes in demand, ensuring that businesses can meet customer needs effectively.
Key Features of Automated Systems
Most automated inventory replenishment and order management systems offer the following core features:
- Inventory tracking and management: Real-time monitoring of stock levels, location, and expiry dates.
- Automated order processing: Automatic generation of purchase orders, based on pre-defined thresholds and reorder points.
- Order fulfillment optimization: Allocation of orders to specific warehouses or distribution centers to ensure efficient delivery.
- Demand forecasting: Predictive algorithms that analyze historical data to anticipate future demand and adjust inventory levels accordingly.
- Reporting and analytics: Comprehensive data dashboards that provide insights into inventory performance, order trends, and customer behavior.
Implementation Considerations
Before implementing an automated system, businesses should consider the following factors:
- Business needs and goals: Clearly define the specific challenges and opportunities that the system should address.
- Integration with existing systems: Ensure seamless integration with existing software applications, such as ERP systems and customer relationship management (CRM) platforms.
- Cost-benefit analysis: Evaluate the initial investment costs and compare them to the potential savings and improvements.
- Training and support: Provide adequate training for staff to ensure smooth operation and effective utilization of the system.
Conclusion
In an era of constant change and increasing customer expectations, automated inventory replenishment and order management systems are indispensable tools for businesses looking to enhance efficiency, reduce costs, and improve customer satisfaction. By leveraging advanced technology and intelligent automation, organizations can achieve greater control, visibility, and responsiveness, positioning themselves for sustainable growth and success.
Reduced Inventory Costs and Improved Efficiency
In today’s competitive business landscape, companies are constantly seeking ways to reduce costs and improve efficiency. One critical area for optimization is inventory management. Excess inventory ties up valuable cash flow and increases storage costs, while insufficient inventory can lead to lost sales and customer dissatisfaction. Fortunately, with the help of modern technology and strategic approaches, businesses can achieve a delicate balance between supply and demand, resulting in significant savings and improved operational performance.
Benefits of Effective Inventory Management
Effective inventory management offers numerous advantages, including:
- Reduced inventory carrying costs: By minimizing excess inventory, companies can lower storage costs, insurance premiums, and obsolescence risks.
- Improved cash flow: Less inventory means less capital tied up, freeing up funds for other investments or operational expenses.
- Enhanced customer satisfaction: Meeting customer demands promptly and efficiently leads to higher customer satisfaction and loyalty.
- Increased productivity: Optimized inventory levels streamline internal processes, allowing employees to focus on value-added activities.
- Reduced waste: Minimizing stockouts and minimizing obsolete inventory reduces waste and environmental impact.
Strategies for Effective Inventory Management
Implementing effective inventory management strategies requires a multifaceted approach, encompassing the following:
- Demand forecasting: Accurate forecasting helps anticipate customer demand, enabling companies to adjust inventory levels accordingly.
- Inventory tracking and control: Real-time inventory tracking systems provide accurate data on stock levels, allowing for timely replenishment and adjustments.
- Inventory optimization: Utilizing inventory management software to analyze data and optimize inventory levels based on demand patterns, lead times, and other factors.
- Just-in-time (JIT) inventory: This strategy aims to receive materials and components just as they are needed for production, minimizing inventory carrying costs.
- Supplier relationship management: Building strong relationships with suppliers can ensure timely and reliable delivery of goods, contributing to efficient inventory management.
Conclusion
Reduced inventory costs and improved efficiency are crucial for any business seeking sustainable growth and profitability. By implementing effective inventory management strategies, companies can unlock significant financial savings, enhance customer satisfaction, and optimize overall operational performance. Through the utilization of advanced technology, data-driven insights, and strategic partnerships, businesses can achieve a fine balance between supply and demand, ensuring that they have the right inventory at the right time, minimizing costs, and maximizing efficiency.
Enhanced Warehouse Management and Optimization
In today’s competitive business environment, efficient warehouse management is crucial for achieving operational excellence and driving profitability. With the rise of e-commerce and the increasing demand for faster delivery times, businesses need to streamline their warehouse operations and optimize their processes to stay ahead of the curve.
Warehouse management systems (WMS) have evolved significantly over the years, offering a wide range of features and functionalities to enhance warehouse efficiency. These systems provide real-time visibility into inventory levels, track goods movement, manage order fulfillment, and optimize space utilization. By leveraging advanced technologies such as artificial intelligence (AI), machine learning (ML), and the Internet of Things (IoT), modern WMS solutions can further automate processes, reduce errors, and improve overall warehouse performance.
Here are some key areas where enhanced warehouse management and optimization can make a significant impact:
- Inventory Management: Accurate inventory tracking and forecasting are essential for avoiding stockouts and overstocking. WMS solutions can help businesses optimize inventory levels, manage stock rotation, and track product expiry dates. By integrating with enterprise resource planning (ERP) systems, WMS can ensure seamless inventory management across the supply chain.
- Order Fulfillment: Efficient order fulfillment is critical for meeting customer expectations. WMS can automate order picking, packing, and shipping processes, reducing manual effort and minimizing errors. By leveraging robotics and automated guided vehicles (AGVs), businesses can further streamline order fulfillment operations.
- Space Optimization: Space is a valuable asset in a warehouse. WMS can analyze space utilization and identify opportunities for optimization. By implementing dynamic slotting algorithms, businesses can maximize storage capacity and minimize travel distances for warehouse staff.
- Labor Management: Effective labor management is crucial for ensuring productivity and efficiency. WMS can track worker performance, optimize task assignments, and provide real-time insights into labor utilization. By integrating with time and attendance systems, businesses can improve labor management and reduce labor costs.
- Visibility and Reporting: Real-time visibility into warehouse operations is essential for making informed decisions. WMS solutions provide comprehensive dashboards and reports that offer insights into key performance indicators (KPIs) such as order fulfillment rates, inventory turnover, and labor productivity. This data can be used to identify areas for improvement and drive continuous optimization.
By implementing enhanced warehouse management and optimization strategies, businesses can achieve significant benefits, including:
- Reduced Costs: Optimized warehouse operations can lead to lower inventory carrying costs, reduced labor expenses, and improved efficiency.
- Improved Customer Satisfaction: Faster order fulfillment and accurate delivery times can enhance customer satisfaction and loyalty.
- Increased Profitability: By streamlining operations and reducing costs, businesses can increase profitability and gain a competitive advantage.
- Enhanced Agility: With real-time visibility and data-driven insights, businesses can respond quickly to changing market conditions and customer demands.
In conclusion, enhanced warehouse management and optimization are essential for businesses seeking to improve efficiency, reduce costs, and enhance customer satisfaction. By leveraging advanced technologies and best practices, businesses can transform their warehouse operations and unlock significant potential for growth and profitability.
Improved Order Fulfillment and Customer Satisfaction
In today’s competitive business environment, delivering excellent customer service is crucial for success. One of the most important aspects of customer service is order fulfillment. Order fulfillment refers to the entire process of receiving, processing, and delivering orders to customers. A streamlined and efficient order fulfillment process can significantly improve customer satisfaction, increase repeat business, and boost overall profitability.
Here are some key strategies to improve order fulfillment and customer satisfaction:
Optimize Inventory Management
Efficient inventory management is essential for ensuring that products are available when customers need them. This involves accurately forecasting demand, managing stock levels, and minimizing stockouts. Implementing a robust inventory management system can help businesses track inventory levels in real-time, automate reorder points, and reduce the risk of stockouts.
Streamline Order Processing
A streamlined order processing system can significantly reduce the time it takes to fulfill orders. This involves automating tasks such as order entry, order confirmation, and order tracking. By using technology such as enterprise resource planning (ERP) systems and order management systems (OMS), businesses can automate order processing, improve accuracy, and minimize errors.
Enhance Shipping and Delivery
Fast and reliable shipping is critical for customer satisfaction. Businesses should offer a variety of shipping options, including standard shipping, expedited shipping, and same-day delivery. They should also track shipments in real-time and provide customers with updates on the status of their orders. Partnerships with reputable shipping carriers and implementing a system for order tracking can ensure timely and efficient delivery.
Provide Excellent Customer Support
Providing excellent customer support is crucial for resolving any issues that may arise during the order fulfillment process. Businesses should offer multiple channels for customer support, such as phone, email, and live chat. They should also have a team of knowledgeable and responsive customer service representatives who can quickly address customer concerns.
Measure and Improve
Regularly measuring and tracking key performance indicators (KPIs) related to order fulfillment is essential for identifying areas for improvement. Businesses should track metrics such as order fulfillment time, on-time delivery rates, and customer satisfaction scores. Analyzing these metrics can provide valuable insights into the effectiveness of the order fulfillment process and identify areas for optimization.
By implementing these strategies, businesses can improve their order fulfillment process, enhance customer satisfaction, and gain a competitive advantage in the market. A focus on streamlining processes, utilizing technology, and providing excellent customer support will ensure that customers have a positive experience and are likely to return for future purchases.
Integration with Other Business Systems
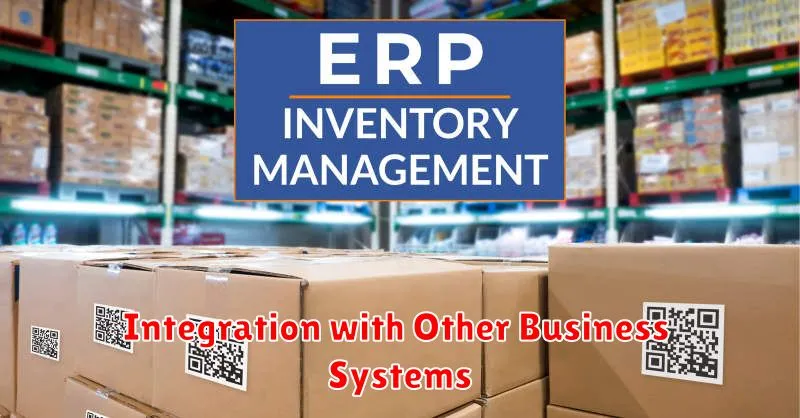
The ability to integrate with other business systems is a crucial factor for any successful software solution. [Software Name] is designed with a focus on seamless integration, allowing businesses to connect their existing systems and streamline their operations.
Key Integration Features:
- API Integration: [Software Name] offers a robust API that enables developers to connect the platform with other applications and services.
- Pre-built Connectors: [Software Name] comes with pre-built connectors for popular business systems like CRM, ERP, and accounting software, simplifying the integration process.
- Data Synchronization: The platform supports real-time data synchronization, ensuring that information is always up-to-date across all integrated systems.
Benefits of Integration:
- Improved Efficiency: Automation of data transfer and processes, reducing manual effort and errors.
- Enhanced Data Visibility: Access to consolidated data from various systems, providing a holistic view of business operations.
- Streamlined Workflow: Integration eliminates data silos and allows for smooth transitions between different systems.
- Increased Productivity: Employees can focus on core tasks, as repetitive data entry and manual processes are automated.
With its comprehensive integration capabilities, [Software Name] empowers businesses to create a connected ecosystem that optimizes their workflows, improves efficiency, and drives growth.
Case Studies: ERP Success in Inventory Management
Inventory management is a crucial aspect of any business, especially for those with complex supply chains. Effective inventory management ensures that businesses have the right amount of inventory on hand to meet customer demand without incurring unnecessary costs due to overstocking or stockouts. Enterprise Resource Planning (ERP) systems have emerged as a powerful tool for optimizing inventory management, providing real-time visibility into inventory levels, facilitating accurate forecasting, and enabling streamlined processes.
This article presents several case studies that showcase the successful implementation of ERP systems for inventory management, demonstrating how these systems have transformed operations and improved efficiency.
Case Study 1: Retail Giant Streamlines Inventory with ERP
A leading retail chain faced challenges with managing its vast inventory across numerous stores. Inaccurate inventory data, stockouts, and overstocking were common occurrences, leading to lost sales, customer dissatisfaction, and increased costs. The company implemented an ERP system that integrated with their existing point-of-sale (POS) system, providing a centralized platform for managing inventory across all locations.
The results were significant. The ERP system enabled the retail giant to:
- Real-time visibility into inventory levels across all stores, reducing stockouts and overstocking.
- Accurate forecasting based on historical sales data and seasonal trends, optimizing inventory levels and reducing waste.
- Automated purchase orders, minimizing manual errors and improving efficiency.
- Improved supplier relationships through streamlined communication and collaboration.
The ERP implementation led to a substantial reduction in stockouts and overstocking, boosting sales and customer satisfaction. It also resulted in significant cost savings through reduced inventory carrying costs and improved purchasing efficiency.
Case Study 2: Manufacturing Company Optimizes Production with ERP
A manufacturing company struggled to keep up with fluctuating demand, often experiencing production delays and missed deadlines due to inefficient inventory management. Their manual inventory tracking system lacked real-time information and led to inaccurate forecasts. To address these challenges, the company deployed an ERP system that integrated with their manufacturing execution system (MES).
The ERP system enabled the manufacturing company to:
- Track materials usage in real-time, improving production planning and reducing waste.
- Automate inventory replenishment based on production schedules and demand forecasts.
- Monitor inventory levels across all stages of production, ensuring timely delivery of finished goods.
- Reduce production downtime by identifying potential bottlenecks and optimizing material flow.
The ERP implementation significantly improved production efficiency, reduced lead times, and minimized inventory carrying costs. The company also experienced an increase in on-time deliveries, enhancing customer satisfaction and loyalty.
Conclusion
These case studies demonstrate the transformative power of ERP systems in inventory management. By providing real-time insights, automating processes, and enabling data-driven decisions, ERP systems empower businesses to optimize their inventory levels, improve efficiency, and achieve significant cost savings. As businesses continue to face complex supply chain challenges, investing in an ERP system for inventory management remains a strategic decision for success.
Choosing the Right ERP for Your Inventory Needs
Inventory management is a critical aspect of any business, and choosing the right Enterprise Resource Planning (ERP) system can significantly impact your success. A well-chosen ERP can streamline your inventory processes, improve efficiency, and ultimately boost profitability.
However, with so many ERP solutions available, choosing the right one for your inventory needs can feel overwhelming. To make the best decision, it’s crucial to consider several factors:
Identify Your Business Requirements
Start by understanding your specific inventory needs. What are your pain points? Are you struggling with inventory accuracy, order fulfillment, or stock forecasting?
Consider the following questions:
- What are your current inventory management practices?
- What are your future goals for inventory management?
- How many products do you stock?
- What are your inventory turnover rates?
- What are your order fulfillment requirements?
Evaluate Features and Functionality
Once you have a clear understanding of your needs, research ERP solutions that offer the features you require. Look for systems that provide:
- Inventory tracking and management: Real-time visibility of inventory levels, location, and movement.
- Purchase order management: Automate purchase order creation, tracking, and approval.
- Demand forecasting: Analyze historical data to predict future demand and optimize inventory levels.
- Warehouse management: Manage warehouse operations, including receiving, picking, packing, and shipping.
- Inventory optimization tools: Techniques like ABC analysis and cycle counting to streamline inventory management.
Consider Scalability and Integration
Choose an ERP system that can grow with your business. Ensure it can handle increasing inventory volume, complexity, and demand. Consider integration with your existing systems, such as your accounting software, e-commerce platform, and CRM.
Seek Industry Expertise
Some ERP solutions cater to specific industries. If your business operates in a niche market, consider an ERP specialized for your industry. This can provide pre-built functionalities and best practices relevant to your industry.
Explore Vendor Options
Research different ERP vendors, compare their offerings, pricing, and customer support. Look for vendors with a proven track record, positive customer reviews, and a strong commitment to ongoing support and updates.
Demanding a Demo
Once you’ve shortlisted a few ERP solutions, request demos from each vendor. This allows you to see the system in action, test its features, and ask questions. Pay attention to user-friendliness, ease of use, and the vendor’s responsiveness to your needs.
Choosing the right ERP is a strategic investment for your business. By carefully considering your needs, evaluating features, and exploring vendor options, you can find an ERP system that optimizes your inventory management, improves efficiency, and helps your business thrive.